With a mission to change
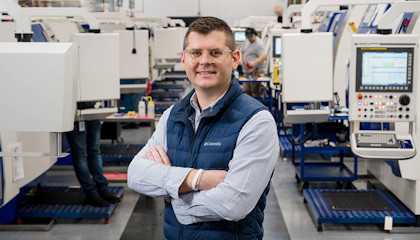
For years, Maxime Coutat guided others on how to improve their operations. A year ago, he moved from power points and consulting to hands-on action by taking over the management at a production unit in Pennsylvania, US. It’s been a successful transformation for all parties.
Frankly put, everything wasn’t top-notch when Maxime Coutat arrived in Reynoldsville, US. Some figures were moving in the wrong direction and the management practices would have benefited from being more in line with the company leadership style, according to Maxime Coutat, Production Unit Director Round Tools at Seco, a Sandvik brand, in Reynoldsville.
In a way, this was good news. “It gave me a great opportunity to apply and make real what I have been preaching to others,” says Coutat, who has spent much of his working life at Seco, guiding others on how to create a healthy and optimized workplace.
For years, Coutat had been traveling the world as an internal consultant to help Seco plants as well as customers improve their operations. The management position in Reynoldsville meant that it was time to deliver; to execute what he helped others visualize while he was running a Production Unit Transformation project at Seco.
“When I arrived, I felt really welcomed by my management team that had a very open mindset and a great willingness to improve things,” he says.
The first challenge was to get the workforce onboard
The first challenge was to get a workforce, not very accustomed to change, to join the journey and share the vision of turning the factory into a people company with a common goal: To transform the Reynoldsville production unit into a benchmark in terms of lean production and company culture.
“This is nothing I can achieve by myself in my office. Hence my job has been to point out the direction and make people understand that this is something we do together,” says Coutat.
He is convinced that everyone is happy to contribute if they are given a chance. “To succeed though, you need to be accepted and people are testing you to figure out if you are up to the job.”
Maxime Coutat
Role: Director Round Tools
Location: Reynoldsville, Pennsylvania, USA
Tenure: Eight years at Seco, three years running the Production Unit Transformation project at Seco. Four years in Manufacturing Transformation. One year in Reynoldsville.
Family: Married to Mathilde, son Gabriel, 2
Favorite hobby: Loves cars (drives a 2023 Volvo S60 Plug-in Hybrid)
Secret superpower: Staying calm
One of his first missions was getting to know the people on the floor. After only a couple of months he knew most people by name. The first big move was to change the organizational structure and make management work closer to the people. Two shift supervisors became one production manager, and a new layer of five managers was introduced.
“It worked well, and we knew that the people we promoted had the competence. I believe that part of the success was that these were the people the others would have chosen as well,” says Coutat.
Niagara Cutters has made round tools in the small rural town of Reynoldsville since 1976. In 2010 the plant became a wholly-owned subsidiary of Seco Tools LLC. Two years later, Seco Tools became part of the Sandvik Group. Many in the workforce of about 90 people have been with the company for longer than 30 years – and some more than 40 years.
Who am I to tell them what their job is?
“So, who am I to tell them what their job is,” says Coutat. “My mission is to make sure everyone knows the direction and knows how to contribute, but many were so used to being told what to do that they weren’t receptive to the changes we proposed,” he says.
The ongoing transformational journey has not been easy. Even so, things are gradually improving. In all places there are early adopters, those that follow, and the group that aren’t as open to new ideas. From Coutat’s experience, those who resist most often become the biggest champions of the project. So, there is no way he is giving up on anybody. He wants to see people succeed.
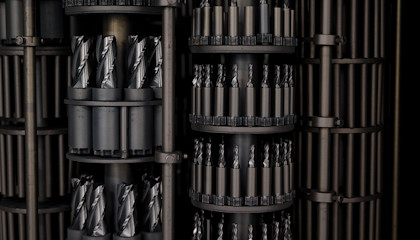
Improving important figures
Timothy Garstka has worked closely with Maxime in this first year on site. He is Production Unit Controller/Finance Manager and the person who held the reins as intermediate manager until Maxime’s arrival. Garstka says there is a clear before and after in relation to Coutat’s start of this transformational journey.
“The intention had for a long time been to bring down the silos between different parties, but this did not succeed until Maxime arrived. He brought a lot of positive energy and put the real focus on the people. If you walk through the hall today, you can feel that the atmosphere is lighter. People are more engaged and happier,” says Timothy.
The KPIs support what they say. A year ago, the quarterly company survey showed that 43 percent of the workforce thought the company had open and honest communication. The latest figure is 74 percent. Over the same time period, employee engagement went from 60 to 71 percent.
To further improve those figures, a new program has been launched, Life 2. The aim with Life 2 is to promote the belief and expectation that people want to contribute once given a chance. To help achieve this, everyone is allocated 30 minutes a day for improvement. Three days a week, 15 minutes of that time is given to training in lean manufacturing, production techniques or inspiring videos or tours of other plants, to improve the everyday work.
My goal is to create a work environment where everyone feels comfortable discussing everything
“We share the strategy with everybody and give each person a focus area and a focus target, to make them see the link between what they are doing every day and the overall goal of the company. We are no longer telling people what to do, we are asking them what their best contribution is,” says Coutat.
Maxime Coutat is not the only one who has tried to drive change at this plant. Timothy Garstka’s explanation as to why Maxime is on a road to success is his patience.
“He listens to people and empowers people to take the actions they are suggesting, and he is good at recognizing individuals for their contributions,” he says.
People will remain in focus on this journey of transformation, to make sure that those still hesitant over change open up to the new ideas.
“My goal is to create a work environment where everyone feels comfortable discussing everything. We still have a long way to go before everyone here is comfortable enough to tell ‘the boss’ what he should do differently, but we are working on it,” says Maxime Coutat.
Three Quick Questions
What is most important for you in your leadership?
"The belief in people and the expectation that everyone wants to contribute when given the opportunity."
How do you excel as a team?
"By having fun and recognizing every small step that’s taking us in the right direction."
How do you contribute to your team and organization?
"By bringing experience and knowledge in operational excellence/lean manufacturing, and by pointing out the vision and making sure that everyone knows how they best can contribute to our getting there."