Nya höjder för nya material
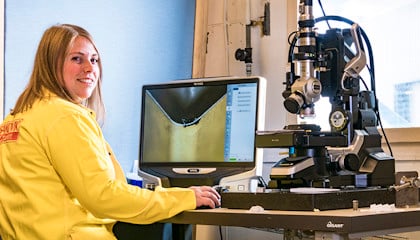
När man utvecklar avancerade verktyg för bearbetning av flyg- och rymdkomponenter räcker det ibland med ett enkelt mikroskop för att förstå hur ett material interagerar med skärverktyget.
Framstegen inom flygindustrin är ofta kopplade till framsteg inom materialområdet - särskilt när det gäller förhållandet mellan styrka och vikt och temperaturbeständigheten hos nya material.
De material som idag väljs för flygmotorer är värmebeständiga superlegeringar, eller HRSA, en komplex cocktail av specialmetaller - nickel, kobolt, järn och vissa TiAl-baserade legeringar (titanaluminid) - som ger avgörande fördelar som att tillåta höga arbetstemperaturer. Många av dessa komponenter har komplexa former och kan 3D-printas. Det skapar i sin tur nya tillverkningsmöjligheter och utmaningar för tillverkare av verktygsmaskiner som Sandvik Coromant.
Tricket att utforma verktyg
Ända sedan bemannade flygplan började flyga med flygplan gjorda av trä och tyg har det gällt för tillverkarna att sänka vikten på flygplanen. Under årens lopp ersattes trä och tyg av aluminium- och titanlegeringar, och så småningom kom kolfiber och kompositer in i bilden.
Jämfört med standardmaterial som järn har dagens HRSA-material, i alla sina kemiska och fysiska permutationer, ombytliga egenskaper. Det krävs mer avancerade verktyg för att skära och färdigställa flyg- och rymdkomponenter i serier som är ekonomiskt och tekniskt lönsamma för tillverkarna.
Flyg- och rymdindustrin kräver extremt höga toleranser för komponenter
Checking wear under the microscope.
"Tricket med att konstruera skärverktyg har alltid varit att öka verktygets livslängd genom att minska slitaget, samtidigt som man uppnår högre skärhastigheter", säger Stina Odelros, Senior R&D Engineer på Sandvik Coromant. "Men flygindustrin kräver extremt höga komponenttoleranser, och ibland finns det ingen möjlighet att byta verktyg i en process, så vi utvecklar ständigt nya verktyg som presterar bättre. Vi måste veta vad våra kunder kämpar med, och sedan försöker vi lösa deras problem."
Ständiga justeringar av material
Odelros förklarar att flygplanstillverkare och leverantörer ständigt justerar material som HRSA och andra legeringsblandningar för att uppnå dessa mål. Förutom viktbegränsningarna måste en motorkomponent också klara utomhustemperaturer på så lågt som minus 60 grader Celsius och interna motortemperaturer på cirka 2.000 grader Celsius.
Att utveckla verktyg för denna krävande bransch är svårt. Den enda metoden att se hur ett verktyg fungerar är att titta på de använda insatserna under ett mikroskop för att se hur de slits. "Vi har inte tillgång till alla dessa material på marknaden, så vi är beroende av samarbeten med viktiga kunder för att få veta hur våra insatser mår", säger Odelros.
Kärnan i FoU-arbetet
Som Odelros förklarar det kan en 3D-printad, smidd eller gjuten flygplanskomponent inte svarvas, fräsas, bearbetas eller borras med ett tidigare använt verktyg. Ibland kan bearbetningen av en stor och dyr motorkomponent ta en vecka eller två, och varje bearbetningspass måste vara kontinuerligt för att undvika strukturella brister. Ett verktygshaveri halvvägs genom processen är inte acceptabelt eftersom det kan leda till att en del går sönder. Och ett komponentfel i en motor kan vara katastrofalt om det inträffar i luften.
Senior R&D Engineer Stina Odelros.
Det Odelros letar efter under mikroskopet, förutom kontrollerat slitage, är storleken på slitaget och om det förekommer mer oförutsägbara typer av slitage som flisor eller frakturer, vilket i värsta fall kan leda till kostsamma produktionsfel.
Detta är den springande punkten i FoU-arbetet. Även om en hårdmetallinsats inte är större än en genomsnittlig fingernagel är möjligheterna att konstruera den - vinklar, substrat, beläggningar, materialsammansättning, kristallstruktur och behandlingar som kemisk eller fysikalisk förångningsdeposition - nästan oändliga. Rätt kombination och mix kan ge skräddarsydda resultat för specifika kundanvändningar.