Hållbara elcyklar med 3D-printing och titan
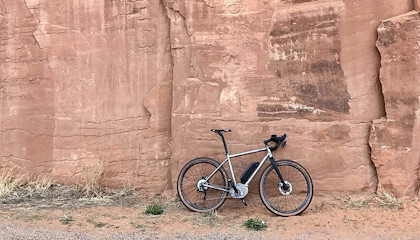
Motornoderna är en av de svåraste delarna att tillverka när det gäller elcyklar i premiumsegmentet. När GSD Global vände sig till Sandvik för att undersöka möjligheten att 3D-printa sina noder i titan blev de glada när de fick reda på att de kunde få en lättare, mer hållbar - och mycket mer energieffektiv lösning.
Under en lång tid har människor varit tveksamma till att ge upp bekvämligheten med sin bil på sina dagliga pendlingsresor. Men med den ökande populariteten för elcyklar (e-bikes) börjar saker och ting faktiskt att förändras. Detta är mer än välkommet med tanke på att koldioxidutsläppen fortfarande ökar - och transportsektorn är den största bidragande orsaken till detta faktum.
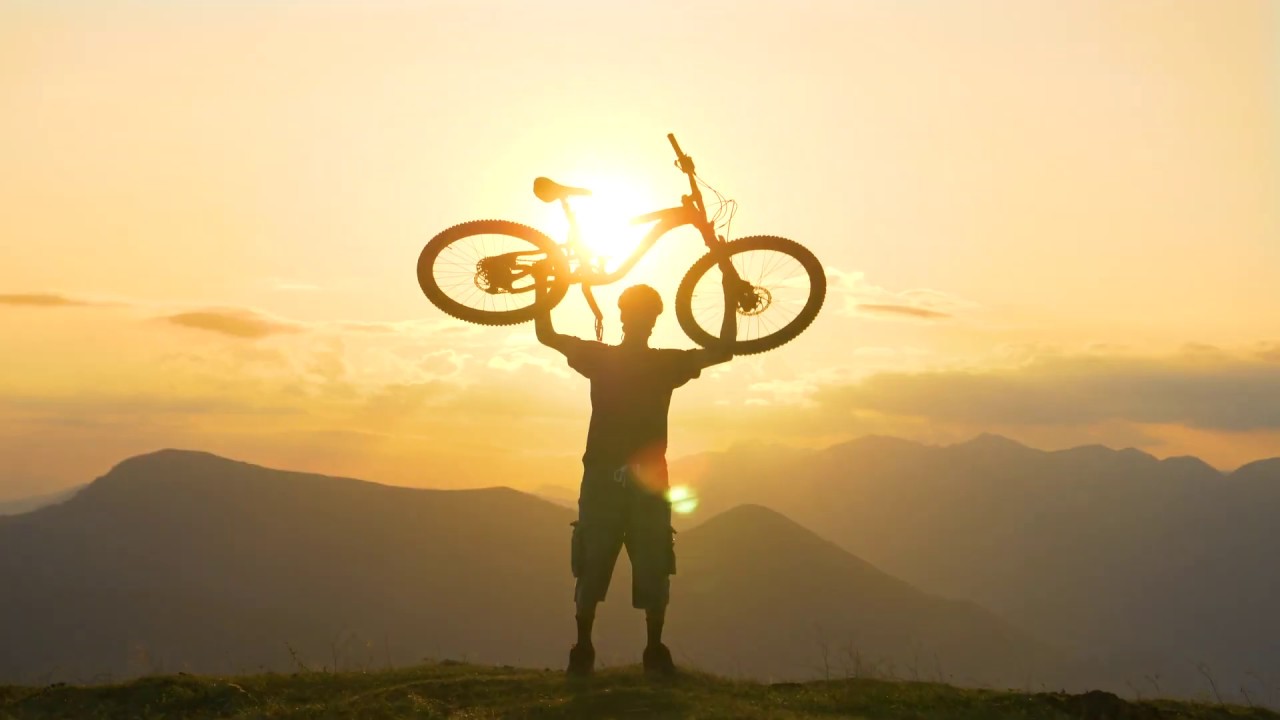
GSD Global är ett konsultföretag inom teknik och design med lång erfarenhet av att skapa premium-elcyklar. Organisationen leds av Zach Krapfl, en ingenjör inom elfordon som är baserad i Paonia, Colorado. Zach är engagerad i global energibesparing och minskad förbrukning av fossila bränslen - och väljer att kombinera cyklar, lätta elfordon och lämplig teknik för förnybar energi som en katalysator för, med hans egna ord, "earth lovin' and a little personal happiness too".
"Jag har märkt att människor som har bytt sitt huvudsakliga transportmedel till elcyklar lever hälsosammare, lyckligare och mer miljövänliga liv", sa han när han höll en föreläsning om framtidens transporter för TEDx.
Som med alla konstformer är avancerade cyklar vanligtvis handgjorda för att tillfredsställa den specifika smaken hos en målgrupp som består av verkliga cykelkännare. Zach Krapfl förklarar:
"Handgjorda cyklar är den typ av produkt som går rakt in i hjärtat - de är konstverk till att börja med. Så om vi kan förse dessa avancerade cykeltillverkare med ett material som gör att deras cyklar håller i 10-20 år och är mer energieffektiva - då är det en gamechanger för dem."
Titan är svårt att bearbeta - men lättare att skriva ut
GSD Global arbetar mot olika OEM-företag (original equipment manufacturers) inom cykelbranschen, men en majoritet av deras designarbete fokuserar på elcyklar. I nästan ett decennium har de samarbetat med Bosch e-bike-system. Tillsammans har de deltagit i flera nordamerikanska cykelmässor och vittnar om att det fram till nyligen har funnits väldigt få elcyklar på marknaden. En del av förklaringen tros vara att de titandelar som till exempel utgör motornoden, som håller fast elmotorn på cykelramen, är mycket svåra att bearbeta med processer som CNC - och dessutom dyra. När GSD Global vände sig till Sandvik för att undersöka möjligheten att 3D-printa sina titankomponenter kunde de till sin stora glädje konstatera att de genom att utveckla designen av motornoderna och anpassa dem för additiv tillverkning faktiskt kunde minska sina kostnader med upp till 75 procent.
Vi är så glada över att kunna dela detta med många varumärken och att kunna börja lägga till fler och fler additivt tillverkade delar i framtiden.
"Det var då vi insåg att vi var något på spåren som inte bara skulle visa sig vara ekonomiskt genomförbart - utan även möjliggöra betydande förbättringar när det gäller kvalitet och energieffektivitet", säger Zach.
Fördelar med hållbarhet
Genom att förse sina OEM-företag med motornoder i titan, 3D-printade av Sandvik, kan GSD Global göra det möjligt för dem att skapa de perfekta elcyklarna som inte bara kommer att kosta mindre och därmed bli mer säljbara, utan också hålla mycket längre. Förutom den ekonomiska lönsamheten innebär möjligheterna att kombinera titanpulver med additiv tillverkning även flera andra fördelar när det gäller hållbarhet, till exempel genom att cyklarna blir lättare och därmed mer energieffektiva.
"Vi ville verkligen lägga till titanets materialfördelar i våra avancerade elektriska framdrivningssystem för elcyklar", säger Zach Krapfl innan han fortsätter att förklara några av de fördelar som han ser med titanets materialegenskaper - till exempel att det är extremt utmattningsbeständigt och kan ge lätthet och lång livslängd.
Efter att ha börjat med motornoderna, som Zach Krapfl kallar en av de svåraste delarna att tillverka, finns det ingenstans att ta vägen förutom uppåt.
"Vi är så glada över att kunna dela det här med många varumärken och att kunna börja lägga till fler och fler additiva delar i framtiden", fortsätter Zach innan han avslutar;
"Och jag längtar efter att få se alla nya Osprey®-metallpulver från Sandvik i framtiden - särskilt från deras nya titanpulverfabrik i Sverige."
Resultat
Lättare, mer kostnadseffektiva och "snabbare att tillverka" motornoder i titan, vilket gör elcyklar mer energieffektiva och hållbara - med ökad prestanda och längre livslängd som resultat.
Designer
Zach Krapfl, GSD Global
Material
Titanlegering, Osprey® Ti6Al4V
Additiv teknik
Pulverbäddsfusion Laser
Efterbearbetning
Värmebehandling och sandblästring