Smarta pulverlösningar bidrar till mindre utsläpp till havs
En stark projektgrupp kännetecknas av självständighet och flexibilitet. Dessa drag var utmärkande när Sandvik och MAN Diesel & Turbo samarbetade för att hitta en lösning för att minska utsläppen från stora lastfartyg.
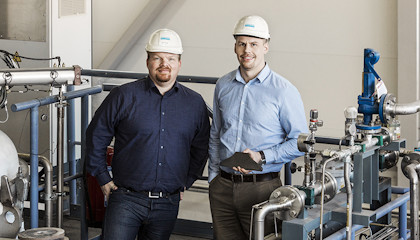
En stor fördel med marin transport är att stora volymer kan transporteras relativt energisnålt. Ändå orsakar utsläpp av svavel, kväveoxider och koldioxid stora problem för marina ekosystem. Hårdare marina regler driver därför på utvecklingen av effektivare motorer.
En minskning av utsläppen innebär en betydande förändring för miljön.
I det nyligen slutförda och EU-finansierade Helios-projektet stödde EU utvecklingen av en dieseldriven tvåtaktsmotor med låg hastighet som fungerar genom direktinsprutning av komprimerad naturgas (CNG). Sandviks del i projektet var att utveckla den mycket viktiga avgasventilen.
− MAN har en överväldigande marknadsandel för marina dieseldrivna tvåtaktsmotorer, så en minskning av utsläppen i deras motorer innebär en betydande förändring för miljön, säger Martin Östlund, Senior R&D Professional inom affärsområde Sandvik Materials Technology.
Jakten på drömkomponenten
Genom att ersätta ett antal nyckelkomponenter ville MAN utveckla en marinmotor som kunde drivas med två olika sorters bränsle – både diesel och naturgas. En kritisk komponent i detta sammanhang var avgasventilen, som behövde kunna stå emot ökad korrosion och högre temperaturer, samtidigt som den utsätts för olika typer av slitage. Medan hela komponenten ska klara höga temperaturer, så är den nedre delen utsatt för värsta korrosionen.
− MAN kom till oss med sin drömkomponent vad gällde kostnad och uthållighet. Vår uppgift var att hitta en lösning som låg så nära denna vision som möjligt, säger Tomas Berglund, specialist på pulverbaserade produkter i nära färdig form och projektledare för Sandviks del av Helios-projektet.
Det är en mycket kostnadseffektiv lösning baserad på en enkel och billig bas, delvis förstärkt med mer avancerade material.
Östlund, Berglund och deras kollegor antog utmaningen med öppna sinnen och snart kom Berglund fram till en idé baserad på en tidigare erfarenhet. Varje ventil väger cirka 50 kilo och det finns inget existerande material som uppfyller alla krav. Att utveckla ett sådant material skulle bli för dyrt.
− Med pulverteknologi utformade vi en komponent med fyra olika material, alla med sina speciella egenskaper, placerade i olika delar av ventilen. Det är en mycket kostnadseffektiv lösning baserad på en enkel och billig bas, delvis förstärkt med mer avancerade material, säger Östlund.
Prisvinnande lösning
Helios-projektet är nu slutfört, och Sandviks tillverkningsteknologi har redan vunnit priser. För att vidareutveckla produktionsekonomin tittar nu gruppen på möjligheten att använda additiv tillverkning i delar av tillverkningsprocessen.
Vi lyckades där andra har försökt och misslyckats.
En av projektets framgångsfaktorer är att Sandvik har alla resurser internt, från omfattande forskning och utveckling till fullskalig produktion. Berglund och Östlund tar också upp den relativt lilla storleken på produktenheten där de jobbar, vilket ger varje projektgrupp en hög grad av självständighet och flexibilitet. Slutligen har kunden varit delaktig från första början.
− MAN:s applikationskunnande i kombination med Sandviks unika material, tillverkningsexpertis och stora resurser var avgörande för den slutliga lösningen, menar Berglund. Vi lyckades där andra har försökt och misslyckats.