Creating the impossible statue
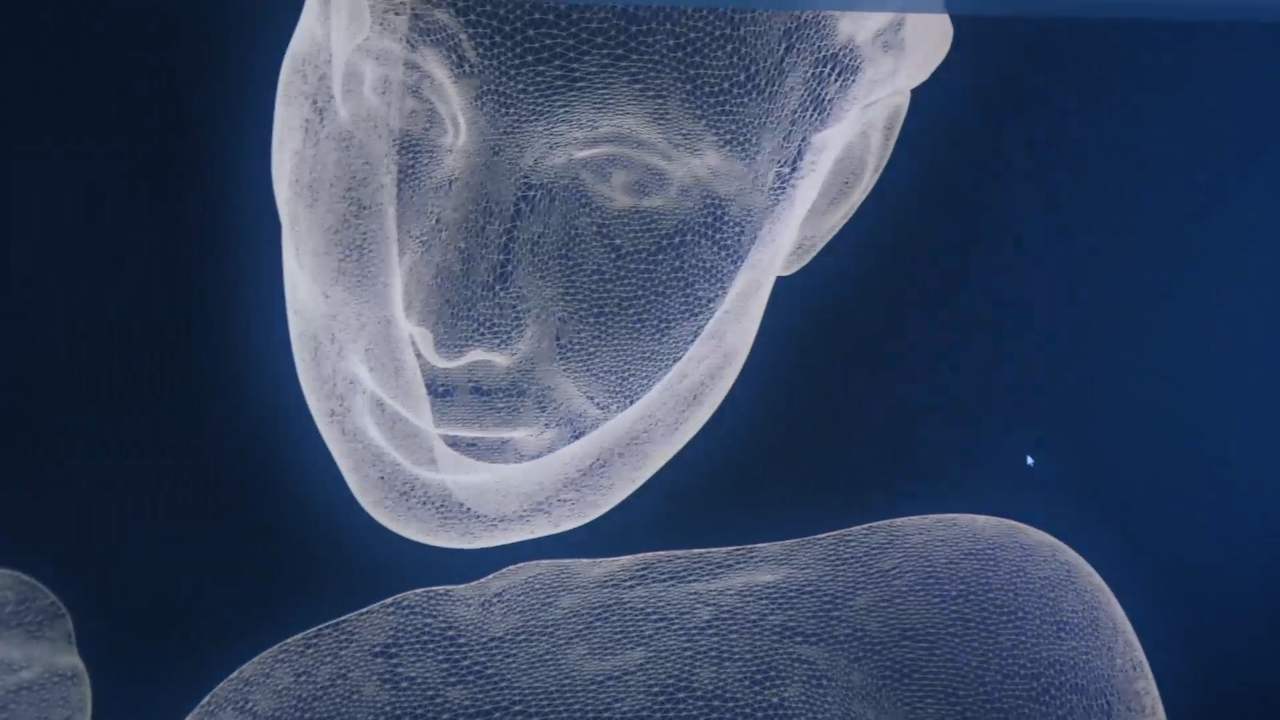
A unique fusion of artistry spanning 500 years from some of the world’s most iconic sculptors was made possible through AI and advanced digital manufacturing solutions from Sandvik.
The Impossible Statue is designed to reflect five historic sculptors. It also showcases what can be achieved when AI and cutting-edge Sandvik software and hardware tools are combined. “By using all our capabilities we could significantly improve manufacturing efficiency, reduce waste and ensure the highest quality in each step of the process,” says Nadine Crauwels, President of Sandvik Machining Solutions.
A combination of different AI programs resulted in a 3D mesh model. “The mesh consisted of nine million polygons with no density. We had to convert this into a solid model that our CAD and CAM programs could work with,” says Henrik Loikkanen, Machining Process Developer at Sandvik Coromant who together with Jakob Pettersson, CAM & Machining Specialist, led the team of Sandvik machining experts that carried out the work.
Digitally perfected
After the conversion was achieved, the team started programming the CNC machines using MasterCam® software. “Originally we planned to make it in one piece,” says Pettersson. “But we realized that the size made it impossible. We had to adapt the parts to fit our CNC machines, so we sectioned the model into 17 components. Each of these had to be designed and programmed, along with the interfaces between them.”
Simulation ensured that we could reach the features we wanted.
Vericut®, a Sandvik proprietary machining simulation and optimization software ensured safe, reliable, and efficient tooling and machining processes. Not a single part of the statue had to be scrapped and remade throughout the process as they had been digitally perfected before the start of machining. The actual machining was made using a wide range of Sandvik Coromant tools for turning, milling, and drilling.
“The complexity meant that verification was a necessity,” says Loikkanen. “There is a lot of trial and error and that is done digitally, prior to machining. Simulation ensured that we could reach the features we wanted when manufacturing the statue and that there would be no collisions.”
Testing time cut to a sixth
With the digital simulations, the total time for testing and verifying the process was cut to a sixth of what would have been required in a manual operation. Additionally, twice as much stainless steel would have been required without the digital simulation tool, if traditional proofing methods had been applied. Thanks to the digital tools for virtual optimization of tool usage and tool paths there was also a very steep development curve throughout the process. Only three simulations were needed to make the last piece compared to 100 simulations for the first one.
We were also able to optimize tool life using the software, enabling us to use less tooling and therefore less energy.
The finished statue is made of stainless steel, weighs 500 kilos, and stands at 150 cm. It deviates from the digital design by less than 30 microns (0.03 mm), a remarkable result considering its size and the complexity of the 3D model. This is the same level of precision demanded in for example the manufacturing of Swiss watches and it was achieved through virtually simulating the optimal way to manufacture the statue, utilizing digital twin technology and technology for optimizing tool paths. And by using Sandvik Coromant tools to make the statue so precisely, very little material was wasted.
“There were no scrapped components due to error. We were also able to optimize tool life using the software, enabling us to use less tooling and therefore less energy. By getting it right from the start with our software we have made it as sustainable as possible,” says Pettersson.
The statue is on display at Tekniska Museet (Sweden’s National Museum of Science and Technology).
Some tools and software used in the making
- Mastercam® The most widely used Computer Aided Manufacturing (CAM) software.
- Vericut® Machining simulation and optimization software.
- CoroPlus® Tool Library creates, stores and manages 3D tool assemblies.
- Coromant Capto® tooling interface Used to connect the arm and head to the torso of the statue.
- Solid round tools from the CoroMill® Plura and Dura families Finishing of all surfaces and features.
- High feed milling cutter CoroMill MH20 Used to machine the bulk of the stainless steel removed.
- Metrolog X4 inspection software was used to compare the finalized statue to the 3D model.
The sculptors who inspired the statue
- The dynamic, off-balance poses of Michelangelo (Italy, 1475–1564)
- The musculature and reflectiveness of Auguste Rodin (France, 1840–1917)
- The expressionist feeling of Germany’s Käthe Kollwitz (1867–1945)
- The focus on momentum and mass exhibited by Kotaro Takamura (Japan, 1883–1956)
- The defiance in the figures of Augusta Savage (USA, 1892–1962).
Find out more
Read more on the website for Sandvik Coromant metal-cutting solutions.