Small part machining saved Knust-Godwin
A long slowdown in the oil industry prompted Texas oil and gas supplier Knust-Godwin LLC to try another direction. When facing new challenges and opportunities following a transition into small part machining, Sandvik Coromant was there to help.
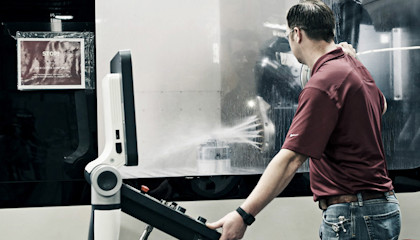
Knust-Godwin, a division of Schoeller Bleckmann Oilfield Equipment AG, is a precision machining company located in Katy, Texas. It specializes in large, complex parts for oilfield instrumentation. But with the recent downturn in the oil industry, Knust-Godwin management agreed the company should work to diversify its customer base.
Used to high-stakes machining
Many of the machine tools in its 22,000-square-metre facility are larger than a tractor-trailer and are able to drill holes up to 9.5 metres deep, turn shafts nearly 6.4 metres long, and mill parts 11 metres across. Yet when the opportunity to machine wristwatch parts came along – some smaller than 10 mm in diameter – Knust-Godwin management said “Why not?".
VERO Watches was struggling with fit and finish problems on prototypes from a local machine shop. It was looking for an alternate source and contacted Knust-Godwin that soon realized that the stainless steel, of which the watch bodies were made, was destroying tools quickly enough that acceptance of future orders was in question.
“I don't mind challenges,” says programmer Chris Hurst. “We’re used to high-stakes machining. But our tool life on the prototypes run was so poor, most of the tools couldn’t complete a single part without needing to replace it. We had to do something different.”
It came out to an 8,000 percent productivity increase per tool.
VERO Watches enthusiastically accepted the prototypes, and Knust-Godwin was soon facing an order for 105 complete watch sets. They called Grant Gregory, account productivity engineer for Sandvik Coromant, who recommended several changes. Tool holders were replaced with Sandvik Coromant’s CoroChuck® 930 high-precision hydraulic chucks. Instead of a solid carbide endmill, roughing was done with a Sandvik Coromant CoroMill® 390-07.
“It was an unbelievable improvement,” says Hurst. “Feeds and speeds, depth of cut – everything was the same, except the one Plura endmill was actually doing 90 percent of the finishing work on the outside of the part. It came out to an 8,000 percent productivity increase per tool.
“We’d long suspected that better tooling would make a difference, but never had this sort of head-to-head comparison.”
Read more about small part machining at the Sandvik Coromant website