Researching the future
A brand new research and development center for additive manufacturing in Sandviken, Sweden, paves the way for exciting new products and methods as well as new business opportunities. What is close to impossible to manufacture today may very well be ready for mass production tomorrow.
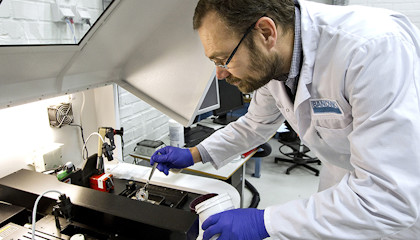
In the new laboratory for additive manufacturing, commonly known as 3D printing, a strong team of researchers, designers and technicians will, with the help of several different kinds of machinery for multiple additive processes and methods, explore new possibilities for existing products as well as future products and production methods.
"The investment in additive manufacturing creates opportunities to produce products that have been nearly impossible to make, and in a reasonably productive way," says Mikael Schuisky, Operations Manager for the new Additive Manufacturing Center.
One industry that has already explored the advantages of this technology is aerospace, where there is a huge demand for lightweight framework structures. A weight reduction of one kilo of an airplane saves 3,000 USD in fuel a year. Also within the medical field, additive manufacturing has achieved major scientific achievements with a growing production of custom-made parts for implants.
"Additive manufacturing makes it possible, to take one example, to create the right porous surface for the body tissue to grow on a hip prosthesis," says Schuisky.
With our expertise and knowledge in metallurgy, in combination with our advanced portfolio of metal powders, we will certainly be in the forefront.
Mikael Schuisky
However, it is too early to tell where the investment in additive manufacturing will take Sandvik. “The new center will provide new tools to evolve and elaborate,” Schuisky says. “Our work ahead will show what products and designs fit these specific manufacturing techniques, and which ones are better suited for current production methods.”
One project he can reveal is the ongoing work with a tool holder for the metal cutting industry, one of many promising projects in the pipeline. Spare parts produced on-site for customers is another vision that has become a reality. Offshore industries, such as oil platforms, cannot carry a huge stock of spare parts. With a 3D printer, this could be quickly fixed, saving time when a part needs to be replaced and the delivery time is otherwise long, due to geographical or other reasons.