A tale of two tusks
When Spike the elephant broke his tusks, the keepers at Calgary Zoo got a little innovative dental help from their friends.
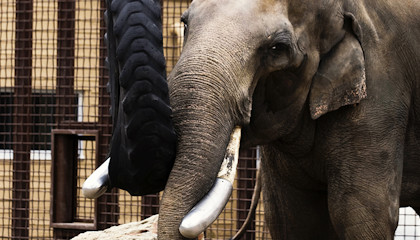
Spike likes to play rough. Whether it is tossing truck tires high in the air or wreaking havoc with the watering system, this 5,500-kilogram (12,000-pound) Asian elephant has earned a reputation of an inquisitive giant. Unfortunately, Spike’s sense of curiosity sometimes gets him into trouble.
Spike moved to the Calgary Zoo in Alberta, Canada, in 1992, after Hurricane Andrew damaged his birthplace home at the Miami Zoo in Florida in the U.S. His first encounter with the dentist’s chair was in 2002, when the roughhousing teenager broke his left tusk on a tire swing, an event that earned him a shiny new stainless steel crown.
Six years later, Spike broke his other tusk, so severely that zoo veterinarians were concerned about the possibility of infection. Dr. Doug Whiteside, the Calgary Zoo’s senior staff veterinarian, says it is not uncommon for male elephants to wear down or break their tusks, but problems can occur if the sensitive pulp is left exposed. The area needs to be protected with a temporary cap until the tooth can grow out away from the pulp.
Luckily, the playful pachyderm had friends and benefactors willing to lend a helping hand. Whiteside contacted the Southern Alberta Institute of Technology, also known as SAIT Polytechnic, the same institution that helped with Spike’s first set of artificial tusk caps. And while the original prostheses worked quite well – until Spike sheared one off, that is – the decision was made to develop more accurate tusk caps with respect to shape and size of the tusks, rather than the approximated curved versions machined in 2002.
Using the same fiberglass material a human doctor employs to wrap a broken leg, they cast mirror images of Spike’s tusks and sent them to SAIT. The inside surfaces were scanned and the data transferred to CAD software for solid modeling.
That is when Mike Desjardins stepped in. Desjardins is President of Lab Machine Works Inc., a local machine shop with greater knowledge of prosthetic elephant tusk machining than anyone in Alberta. “I was commissioned to machine the first set,” he says. “Because of the curved shape and the greater size, these were quite a bit more difficult to produce.”
Starting with a pair of 316 stainless steel blanks 20 centimeters (eight inches) in diameter and 58 centimeters (23 inches) long, Desjardins was facing 230 kilograms (500 pounds) of metal removal. He reached out to Sandvik Coromant Area Sales Manager Jim Cordoviz and Area Representative Scott Jensen, who donated a pair of milling cutters.
“Working with SAIT, we split the blanks lengthwise and welded fixturing tabs on each half,” Desjardins explains. “Each piece was then clamped into a Haas VF-2 vertical machining center. The G-code was produced by processing the solid models through our MasterCAM programming system. Even so, it took more than 120 hours to finish the project.”
“I think this project was a great example of how innovative partnerships can work, in this case to enhance the health and welfare of a wonderful species,” Whiteside says. “The community really came together for Spike, and we are very appreciative of the expertise, time, and material donated for this project.”