Moving from compliance to business advantage
Stuart Evans has been working around heavy industry since his university years. He’s spent most of this time in mining, but he has also worked in oil and gas and nuclear facilities. Environment, Health and Safety (EHS) issues are therefore nothing new for the Global Head of Environment, Health and Safety, Sandvik Group.
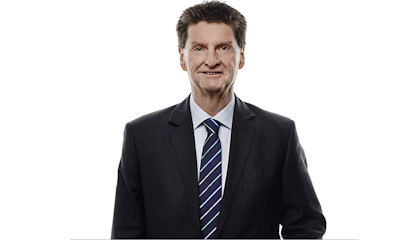
How does Sandvik work with EHS from a customer perspective?
Our customers often look for a supplier who has EHS values and a culture at least as strong as their own. They will typically look at the things we say in our Sustainability Business Report and marketing information and then compare it with what we actually do. You can say that they evaluate whether we walk the talk. If we pass this test, they will start looking at how well we have built these values into our product or service offering to the market. To judge this, a customer may look at, for example, whether we have eliminated the major safety issues associated with an underground loader, or how much of our tubing is made from recycled materials.
Has Sandvik always had this view on EHS?
During its long history Sandvik has probably always thought about EHS in line with current community and market expectations. What has changed in recent times, certainly over the past ten years, is the rate at which those expectations have increased. It is no longer good enough to think about EHS as an added-on part of our business. Nor is it good enough to just meet the legislated rules and regulations. I think of EHS as a culture change journey. The part of the journey we find ourselves on now is about fully integrating EHS into every aspect of our daily work and about seeing EHS as a business advantage rather than a compliance issue.
Do you measure the progress somehow?
We measure a lot of different aspects of EHS on a regular basis – both the outcomes, such as injury rates and carbon dioxide emissions, and the preventive activities. Every business area has formulated plans on how it will improve its way of working with EHS issues. We follow up these plans on a quarterly basis and report progress to the Group Executives. Our major competitors are all starting to change their way of working and are communicating more about EHS as well, so we need to keep up our momentum and always try to be one or two steps ahead.
Will we work differently with EHS in the future?
Most definitely. As the world changes, EHS must adapt more quickly for us to meet the changing community expectations. As an example, new technology and improved data transfer rates make higher levels of automation possible. This makes it possible to move more people away from the more dangerous and remote workplaces. Instead of operators working in deep mines, they can run machines from a safe location on the surface. This transition has already started.