Climate-smart manufacturing
The majority of scientists agree that human behavior is the major driving force behind climate change. Therefore, the task to change environmental impact lies in the hands of humans and companies.
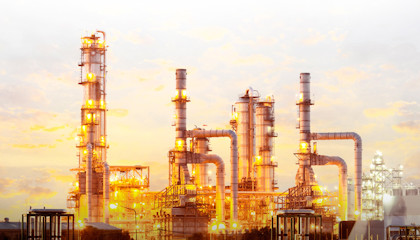
Global warming is one of the world's biggest challenges. In order to meet climate goals, the world must substantially reduce carbon emissions. How can energy-intensive companies such as Sandvik contribute? Modern technology helps us to build more climate-smart plants and offices, as well as reduce our house hold emissions, but the goal is also to help customers become more energy-efficient.
"By offering highly productive products that provide high energy efficiency, we can help our customers reduce their impact on the environment," says Christina Båge-Friborg, Head of Sandvik Sustainable Business.
Stig Jansson, Technical Manager at the brand new climate-smart Sandvik Coromant center in Sandviken, Sweden, agrees. He shows one of the center's new machines, which is much smaller than some of the others.
"This is one example where we've developed machining methods that require less energy," Jansson says. "With the right tools and methods, we can help our customers produce their components on a smaller machine with significantly lower impact and still reach the same result as with a large machine."
One area where Sandvik Machining Solutions have been in the forefront for many years is the recycling of solid carbide tools. During 2014, Sandvik Coromant recycled 98 percent of sold weight, and actually exceeded 100 percent during Q4 thanks to the fact that they accept all brands in their recycling bins. "Knowing that it requires 70 percent less energy to produce tools from recycled solid carbide than making them from new raw material, it's an obvious thing to do," he says.
Sandvik Materials Technology also focuses on energy-efficient products and services such as energy-efficient heating cassettes for solar panels and corrosion-resistant stainless steel plates for fuel cells. Furthermore, Sandvik Materials Technology has several internal stories to tell. One example is the collaboration with the local energy company in Västerås, Sweden. Through a new technique, the energy company helps the Sandvik unit in Hallstahammar, Sweden, recycle waste energy, which leads to yearly carbon dioxide savings of approximately 1,400 tons.
"The best kilowatt-hours are the ones we are not using," says Nicklas Nilsson, Head of Product Area Strip, Wire and Heating Technology, Sandvik Materials Technology.
"Walking or riding a bike instead of taking the car, turning the light off when you're notin the roomand other things that we can easily do – it all starts with you and me."
The mining industry is extremely energy-intensive and accounts for about 5 percent of the world's consumption of electrical energy. To help mining companies reduce their emissions, Sandvik Mining has designed lightweight trucks and loaders with an intelligent powertrain design, powered by stage IV/tier 4-compliant clean engines that transfer all power to the movement of the truck. This means a lower impact on the environment and at the same time the lowest cost per ton for customers.
Australian mining company Mincor has invested in four new trucks, Sandvik TH551, equipped with an onboard weighing system. The investment allows the company to reduce the number of trucks by about half.
"There is a definite productivity benefit and therefore a cost improvement due to running fewer units to do the same job," says Brett Fowler, General Manager of Operations at Mincor Kambalda. Sandvik's goal is to be one of the most sustainable companies in the industry. To succeed, every little step from each and everyone counts.