Keeping safety in mine
Thanks to Sandvik's automated mining system, Northparkes mine has not only improved safety considerably, but has increased productivity as well.
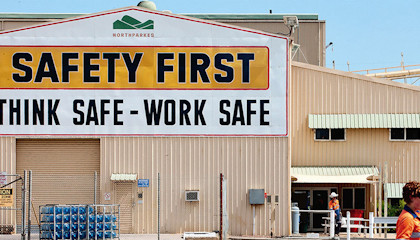
At the Northparkes copper and gold mine in New South Wales, Australia, the staff responsible for underground loading used to start their shift with a meeting, then take a lift underground and prepare for work with the loaders. It took time. Now, they head straight to a surface control room and supervise automated loaders through remote control.
Safer and faster with the automated mining system
It is safer and faster, and we get more tonnes out of the mine", says Matthew Betts, Northparkes' manager for infrastructureand design for the project. "Northparkes, close to the town of Parkes, has already automated its material handling system. Now the mine is gradually introducing Sandvik's AutoMine loading system.
In January, 40 percent of the mine's loading operations were automated. Full implementation is expected by the end of the year. "For us, automation is a key enabler for Northparkes, allowing us to produce at a lower unit cost and to mine deeper, lower-grade ore bodies cost-effectively in the future," Betts says.
Higher production rate
Some of the immediate benefits with AutoMine relate to shift changes and blasting re-entry. On some days, there were periods of up to two hours where no-one was working at manual loader operation level. Now, even when there's no one in the mine, the loaders continue to produce.
"We've probably gone from about 20 or 21 hours a day of utilization up to 23 hours or even more," says Joe Cronin, Northparkes' LHD automation manager. Safety is another major advantage. In an underground loader environment, staff can be exposed to vibration, noise and dust. That may be an even greater problem in other mines and in the future as deposits get deeper and you have to extract ore in more challenging surroundings. "By automating the fleet we remove staff from that environment and bring them to a controlled office environment," says Betts.
Sandvik has put together AutoMine loading as a full package to suit Northparkes' future needs. It includes loader automation and traffic and production management, as well as the interface to the Supervisory Control and Data Acquisition system for monitoring remote operations from a central location.
Sandvik Mining's personnel responsible for the implementation take pride in their achievement and the close working relationship with the Northparkes team. "We maintain all the mobile equipment in the production fleet, plus we are now responsible for the automation infrastructure and the onboard automation equipment on the machines," says Ben Rix, Sandvik Mining's acting Northparkes Mine's performance contract manager. "We work around the clock, 24 hours a day, seven days a week, 365 days a year, to keep the machinery running for production."
Northparkes is part of Rio Tinto, a world-leading mining corporation, and Cronin says the mine has traditionally been regarded as a test mine for technology for Rio Tinto globally. Thus the successful implementation of the AutoMine loading system at Northparkes could set the stage for rolling out the system at other Rio Tinto underground hard rock mines. "We've got a very high level of experience at the mine and very high levels of technical expertise, and we have a large majority of staff who've been here for more than 10 years," Cronin says.
"There's an old expression within Rio Tinto: 'If it doesn't work at Northparkes it's not going to work'."